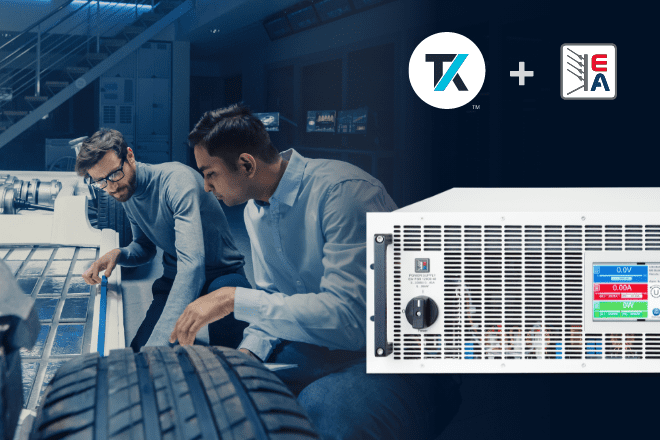
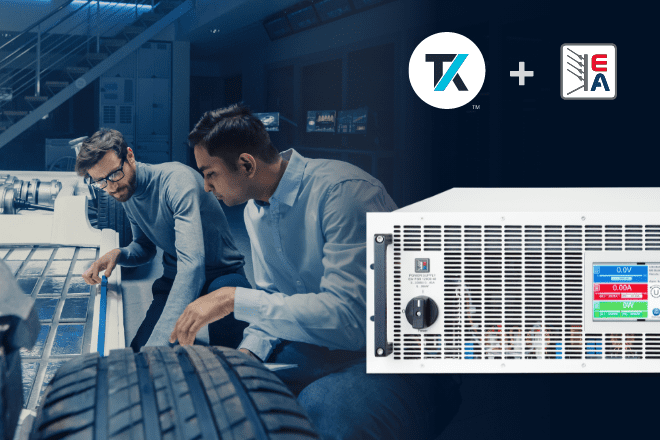
Electrical car battery producers and EV producers are working to beat the 2 largest challenges of electrical mobility: vary and charging time. Inside this framework, testing techniques have to be versatile to adapt to greater voltages and higher-capacity batteries. The next sections present an outline of present and future battery applied sciences for electrical autos. It then examines how battery check techniques can preserve tempo with the event of latest battery packs.
EV battery applied sciences
Lithium-ion batteries are comparatively light-weight, exhibit excessive vitality effectivity, and are much less more likely to overheat at excessive temperatures. In comparison with different battery varieties, Li-ion takes longer to discharge, thereby providing journey ranges as much as 500+ miles on a full cost. In North America and Europe, EV Li-ion batteries make use of both nickel, manganese, and cobalt (NMC) or nickel, manganese, cobalt, and aluminum (NMCA). Broadly utilized in China, lithium-iron-phosphate (LFP) reveals decrease vitality densities, which require bigger battery sizes to supply vitality ranges corresponding to NMC-based batteries.
Underneath improvement, solid-state batteries present nice promise to be used in future EVs. Stable- state batteries can keep away from using the extremely reactive metallic lithium. Electrolytes are stable supplies such polymers, ceramics or glass. Anodes might be graphite or silicon, and cathodes might be nickel-based supplies. Stable-state batteries require much less area and provide greater vitality densities than Li-ion batteries. In consequence, solid-state batteries might double the vary of electrical autos. The solid-state electrolyte permits ions to maneuver extra rapidly between the battery anode and cathode, enabling sooner charging.
One other future different to Li-ion, lithium-sulfur, is just like stable state. Stable-state batteries provide an extended vary than Li-ion batteries and are less expensive to supply. The assumption in Europe is that lithium-sulfur batteries current much less of an affect on the surroundings in comparison with Li-ion batteries made from cobalt.Â
In comparison with Li-ion batteries, graphene batteries are lighter, bodily stronger, and dissipate warmth higher in the course of the cost/discharge cycle, limiting the chance of overheating and fires. Moreover, graphene batteries can retailer bigger quantities of vitality in the identical measurement package deal and recharge sooner. Important challenges to mainstream adoption embody scalability of graphene manufacturing, cost-effectiveness, and integration into current battery manufacturing processes.
Mentioned to be cheap and highly effective, zinc-air batteries ship energy when oxygen oxidizes zinc. Nonetheless, oxidation degrades battery efficiency, a barrier to extensive use of zinc-air batteries.
Rising battery voltage and complete kWh capability
EV battery packs are rising in voltage and capability to handle the journey distance problem. Some autos in the marketplace have 800 V battery packs. Massive autos similar to vans, trains, and airplanes will quickly make use of even greater battery voltages. Greater voltages scale back the present necessities, which reduces the dimensions of the current-carrying wires. Smaller wiring assemblies scale back car weight, contributing to larger car effectivity and longer drive distance.Â
An 800 V battery requires over 200 Li-ion 4.2 V cells, yielding a nominal voltage of 830V. The voltage on the battery can rise an extra 20 to 30 V throughout regenerative breaking, leading to a battery voltage that may attain 860 V. Having a switching energy provide, for instance, with a flyback converter topology, to cost the check system requires a circuit that’s 150 V to 200 V greater than the battery voltage. Subsequent, add in 20% headroom, and the circuit can have a most voltage of round 1.3 kV. At that voltage, a check system will want a supply voltage capability of 1500 to 2000 V to check and cost 800 V and better battery packs. Â
Along with greater voltage EV batteries, battery capability is rising as nicely. No less than one producer is utilizing a 100 kWh battery pack to increase drive distance. To cut back recharge time, firms are growing 250 kW charging techniques that may add as much as 180 miles of drive distance in 15 to twenty minutes.Â
The testing problem
Battery check techniques have to evolve to check the upper voltage and better capability EV battery packs. As indicated, check techniques will want voltages to exceed 1000 V and energy over 250 kW capability to check a battery’s most voltage and its skill to simply accept a excessive present cost charge. A high-voltage and high-power system will allow battery biking to make sure the battery pack meets its voltage-time discharge curve specification and to estimate cycle life beneath quick charging circumstances.Â
Different exams embody:
- Pulse exams that require the battery to ship or soak up excessive present in brief intervals for the evaluation of battery thermal design and state of cost (SOC)
- Drive cycle simulation to evolve to plain drive simulation exams similar to Federal Take a look at Process (FTP-75)
- DC inside resistance to evaluate a battery’s state-of-health (SOH)
- Insulation resistance to determine defects that may scale back battery effectivity and trigger questions of safety.Â
Some check techniques have to be able to vibration and shock testing, which is crucial for the reliability testing of off-road autos. Nonetheless, this testing is a high quality assurance check somewhat than a manufacturing check carried out on all battery packs.Â
Batteries might be operated in cycles with bidirectional energy provides. Units similar to these manufactured by EA Elektro-Automatik, have energy ranges as excessive as 30 kW and 60 kW. With these provides, one 42U excessive check rack can have a 300 kW capability whereas consuming solely 6.5 sq ft of producing flooring area. With EA provides having a novel true autoranging output (or enter) that permits supply (or absorption of full energy right down to 1/3 of the availability’s rated voltage, one 300 kW rack can assist 2.4 kA.Â
Testing massive, high-capacity battery packs necessitates {that a} battery check system has safety options to stop injury to battery packs and the check system. Methods want to watch battery temperature, present security checks to stop reverse polarity connections, and make sure the battery is sufficiently pre-charged to a protected stage earlier than it may well settle for a big cost present.Â
At such high-power ranges, the bidirectional energy provides (or digital hundreds) can save substantial utility prices if they’re regenerative and effectively return absorbed energy to the AC grid. For instance, EA bidirectional energy provides and hundreds can return absorbed vitality with distinctive effectivity—as much as 96.5%.
Performing the heart beat exams and drive cycle simulations requires a check system with quick slew charges and excessive information acquisition charges for information seize. The techniques additionally want waveform technology functionality for the drive cycle simulations.Â
With rising manufacturing volumes, rising throughput is crucial. Whereas the battery pack dictates the velocity of testing, extra check capability can generate elevated throughput. A system that may improve energy capability into the MW vary can improve the variety of batteries examined concurrently to extend throughput. Additional particulars might be present in our white paper, which you’ll obtain freed from cost.
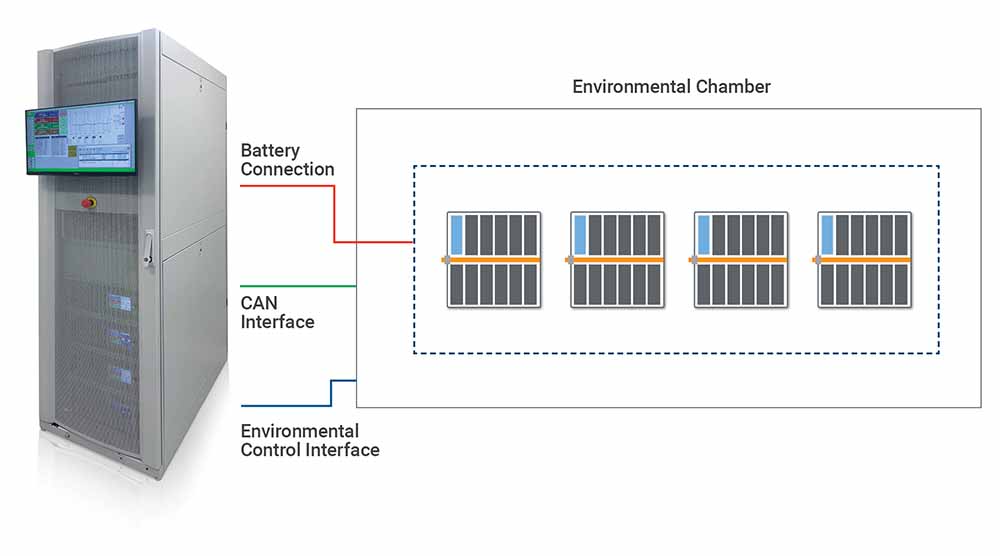
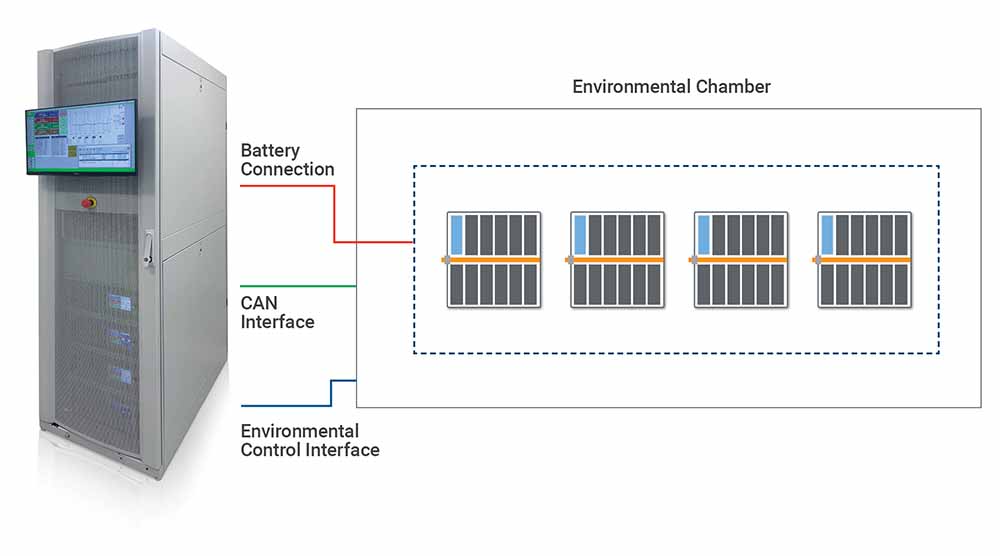
Necessities for the battery check system producers
New EV batteries can be popping out of the lab and onto the market quickly. They may have greater voltages, greater capability, and the flexibility to recharge rapidly. EV battery check techniques might want to have the voltage ranges, quantities of energy, security options, and throughput to check the brand new batteries for a rising EV market. These check techniques will want a return on funding from utility price financial savings and manufacturing overhead financial savings. EA is one battery check system producer that’s addressing these challenges.Â